Three Phase Solar Pump Control with MPPT and VFD
MEDI’s 3 phase solar pump control is an electronic device which is a combination of inverter, MPPT and Variable Frequency Drive (VFD) targeted mainly for solar pumping systems for irrigation. The scarcity and poor quality of electricity supply in rural India leads to use of alternate energy for water pumping systems in Indian agriculture. Solar energy which is abundant in Indian states can be harnessed for this purpose. Keeping this in mind, MEDI has launched this 3-phase solar pump control systems which uses solar energy, does not require batteries and pumps water from early mornings till late evenings, even under cloudy conditions.
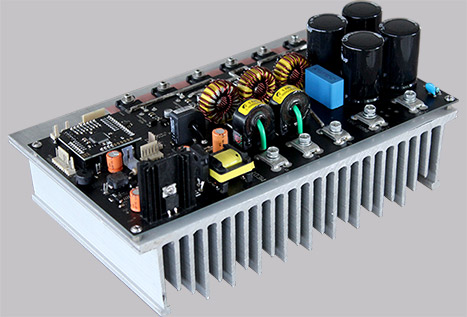
From a panel if you take less current the panel voltage will be high but because the panel current is low the VA will be less. If you take more current, the panel voltage will drop and the VA will be less. But if you take a critical current, the panel voltage and panel current will be high and VA will be much higher. This will vary depending on the sunlight intensity.
In our solar pump controller, the DSP (Digital Signal Processor) will multiply the panel current and panel voltage and vary the PWM duty cycle and modulation frequency to obtain the maximum VA from the panel through out the variation in the intensity of the sunlight. So from the panel we will always get the maximum energy.
Now we got maximum power from the panel, but if we give more voltage to the motor, the slip will reduce and motor will not run at maximum efficiency. If you increase the frequency, the slip will increase and again the motor will not run at maximum efficiency. But at a particular slip the motor will run at its maximum efficiency which will vary depending on lot of factors. So the DSP will sense the maximum efficiency is at what slip and will control the voltage and frequency to ensure that the motor always runs at maximum efficiency.
Because of this our unit will give more water output than any other pump controllers under the same sunlight intensity using same panel and same motor. Only putting MPPT and VFD together cannot achieve this.
The best way to evaluate this is to connect our unit and any pump controller available in the market and test the water output with the same sunlight intensity, same panel and same motor. You can see the water output from our unit will be significantly more.
FEATURES -
- This solar inverter with MPPT VF drive will give maximum torque even at minimum sunlight
- There is no need of any battery, directly connect the panel to the inverter and the output of the inverter can be connected to a three phase motor.
- The DSP will track at which point the maximum power can be extracted from the panel by varying the PWM and modulation frequency so the motor will run always extracting the maximum power from the panel and at a constant torque for the wide range of intensity of sunlight - morning till evening.
- This will give 35% extra energy which results in pumping 35% more water compared with the conventional three phase inverter + three phase pump or DC motor based pump.
SPECIFICATION -
- DSP based intelligent Maximum Power Point Tracking (MPPT) will give 35% more energy from the panel.
- Because of the variable frequency drive (VF drive) the starting current of the motor will come down drastically. So the motor will start even at minimum intensity sunlight - say morning 7 o'clock.
- VF drive will give constant torque for wide range of intensity of sunlight - morning till evening. So water will be continuously pumped from morning till evening
- IGBT based power stage
- PWM frequency - 20KHz
- Pure sine wave three phase current to motor
- Wide range of operating voltage
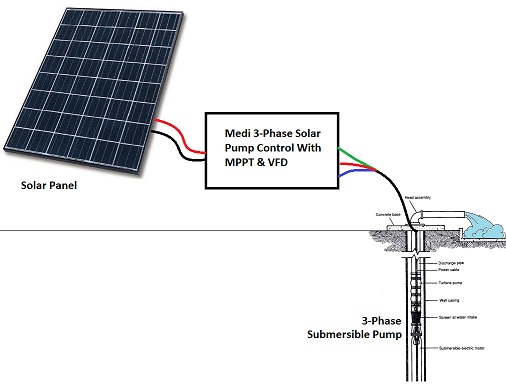
MPPT action - Maximum Power Point Tracking
If a DC motor is used along with the pump there is no MPPT action. If the motor is designed to work at maximum power point during peak sunlight (noon) then at less intensity sunlight (mornings and evenings) the motor will not be at its maximum power point so the full energy is wasted. On the other hand if the motor is designed for maximum power point during less intensity sunlight, it will not be at its maximum power point during noon which again leads to waste of energy. Even though this method is used in many places it is in-efficient.
This system works at its best during any time of the day at any kind of sunlight so effectively we will get 35% extra energy which is being wasted at present using other inefficient methods.
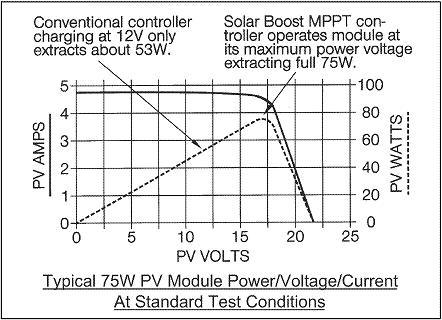
Variable frequency drive eliminates the high starting current of the induction motor
The induction motor has very high starting current which is around eight times of the running current of the motor. If the motor is started with load, the starting current is much higher than this. Without smooth start high wattage panels are required for starting the motors. Because of the smooth start using variable frequency, the motor will start as early as even 6am without taking any starting current. It is practically observed that the starting current will be lesser than the running current from the panel.
Maintaining maximum efficiency of the induction motor by varying VF ratio
The induction motor has maximum efficiency at certain VF ratio. By simply increasing the voltage or the frequency we are reducing the efficiency. If we increase the voltage the slip will reduce so the efficiency and torque will reduce. If we increase the frequency the slip will increase so the efficiency and torque will again reduce. The induction motor has maximum efficiency at a certain slip.
The graph below explains –
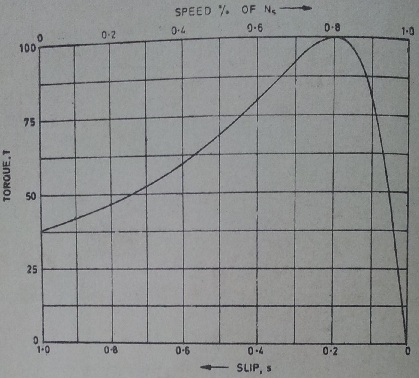
The system runs at maximum efficiency at all the time by constantly maintaining the motor in the right slip which leads to this maximum efficiency.